Maximum production,
minimum space
Spirals for room-temperature cooling or forced cooling, freezing and fermentation. They are manufactured with plastic modular belts with widths ranging from 400 mm to 1,500 mm. Its length can be adapted to the client’s needs and available space, achieving large production yields using minimal space, as it takes advantage of the full height of the location where it is installed.
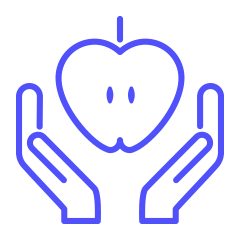
Food safety
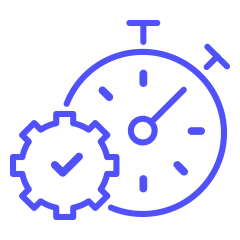
High productivity
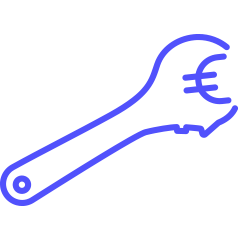
Savings on maintenance and repairs
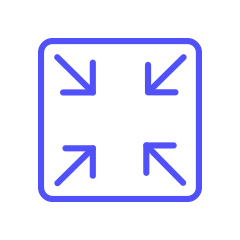
Space optimisation
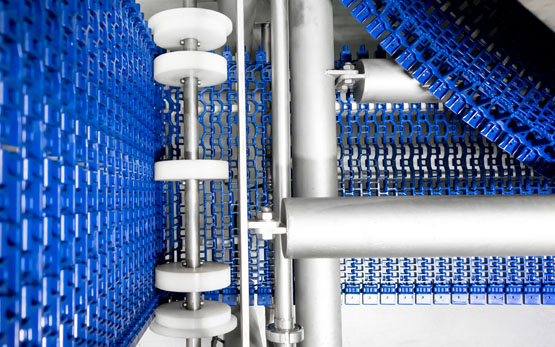
Machinery with stainless steel structures
The spirals are constructed with a stainless steel tubular structure, which facilitates and simplifies their transport, assembly, maintenance and cleaning.
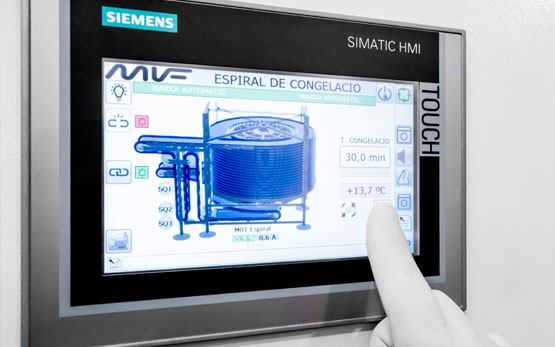
Automation with total control
The operation of the spirals is managed by means of a colour touch screen with icons - its operation is very easy and intuitive.
From this same screen, other conveyors of the same installation may be controlled, along with accessories such as the washing machine or the temperature of the chamber.
Direct Drive DD© Intralox®
spiral system
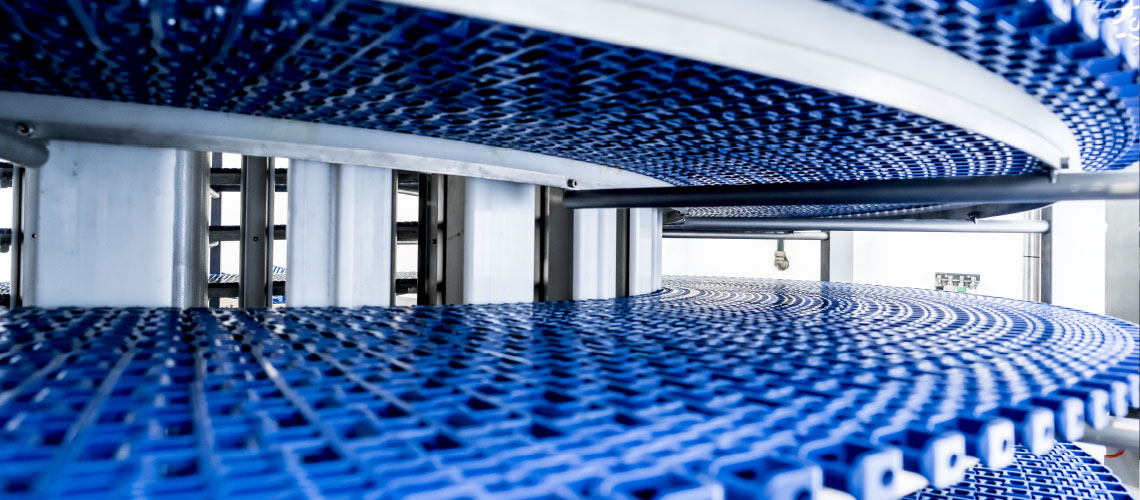
This is a drive system whereby the belt engages directly with the drum so that there is no friction, offering great stability when advancing so that the products maintain their position.
Intralox®
Selfstacker System
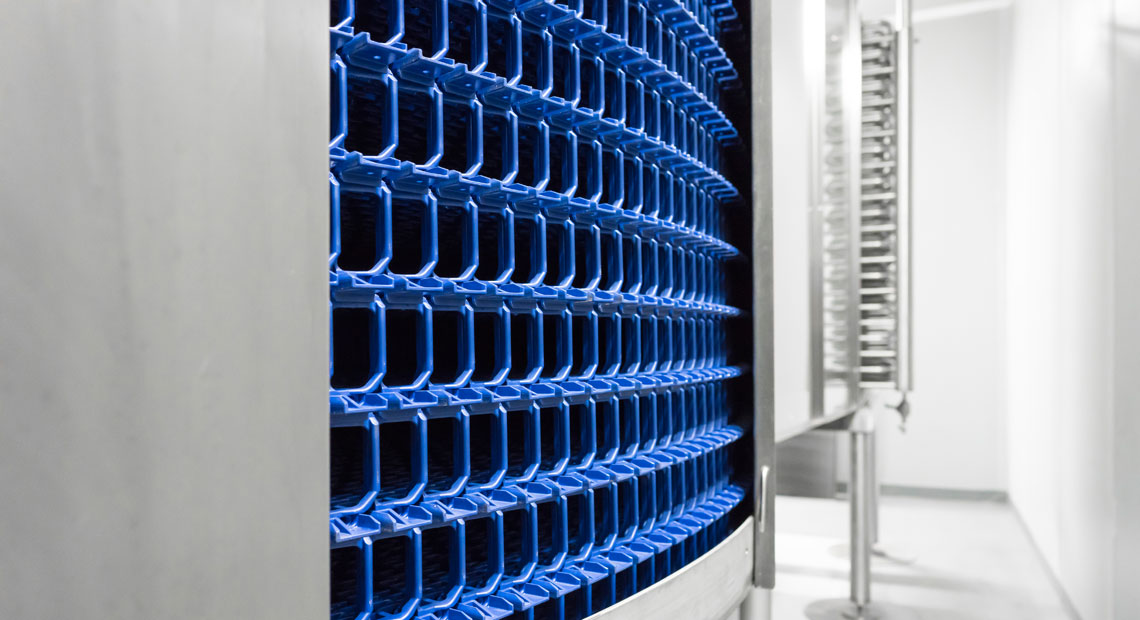
This is a self-stacking belt system that saves up to 30% in height compared to a traditional spiral. Low maintenance, few breakdowns and quick repairs.